大学毕业开始从事IE一职,目前已有4个年头,在这4年时间里,我共经历了两家公司,在第一家公司,我了解并熟练运用了很多IE基础工具,也对精益理念略知皮毛,随着羽翼逐渐丰满,我不满足于每天的日常琐事,渴望更大的舞台来展示自己,就这样来到了第二家公司。在这家公司里,我从一名IE工程师转变为一名IE组长、从一名个体贡献者转变为一名基层管理者、从负责车间的改善工作转变为整个公司的精益生产“带头人”。这4年时间说长不长,说短不短,但足以将我磨练成一名合格的IE人。 场景一 “吴工,没想到简简单单进行个工序重排就把我们工位总是超节拍的问题解决了,明天再来帮我看看其他工序”,这是我还在第一家公司的时候,某天晚上车间班组长对我说的话。这里给大家复现一下当时的情况: 接触过整车厂的人应该都知道,不论是乘用车还是客车,大的工艺流程分为: 冲(压)—焊(接)—涂(装)—总(装)。我当时被分配在焊装车间,产线上有一个工位叫做“仓体封板”,这个工位的主要工作内容是在车身骨架上焊接金属封板,来达到密封仓体的作用,其中有2名焊工需要焊接4块发动机仓封板(如图1): 
图1 其中,封板1、2为A员工焊接,封板3、4为B员工焊接,整条产线的TT为16min,但是员工的CT却达到了18min左右,经常需要工位长去后工位补焊。我通过秒表测定后发现,员工的纯作业时间为16min左右,那么为什么原本纯作业时间在16min的工作,却每一台车都要工作到18min甚至更久?在收集完数据后,我开始了仔细的观察分析,最终发现了问题所在,我们通过图2以及表1的联合分析来更好的还原当时的情况: 
图2 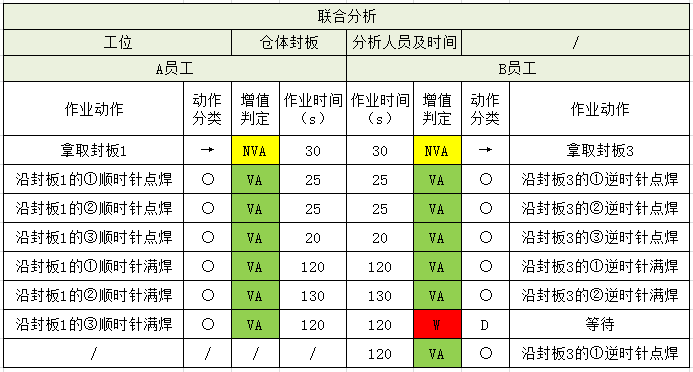
表1 从图2、表1中我们可以看出,当2人都焊接到③位置时,由于狭小的空间无法让两人同时焊接,所以2人中谁先焊接到这条缝隙时,后作业到这的人就需要等待前1个人焊接完成,之后再进行焊接,由于人员的作业时间存在着一定的波动,所以封板2和封板4也有可能会存在这种问题,那么这种等待时间就进一步加长,最终在16min的节拍内,员工无法完成本来能够完成的工作。 找到问题点后,我开始思考如何进行改善,现在看来这种问题属于联合作业当中的串并联工作安排不当造成的等待现象,使用ECRS中的“R”即可解决,但是当时想出这个方案的时候也是思考了好久,最终定下来的方案是A员工先焊接封板1,B员工焊接封板4,之后再分别焊接封板2和封板3,这样就可以把两者相互干涉的动作取消掉,进而消除等待时间。 最终验证的结果正如前面描述的那样,2人均能在规定节拍内完成各自的工作,这个改善算是我独立自主开展的第一个改善,也是建立我改善自信心的重要里程碑。现在每当我给车间班组长培训ECRS的知识时,脑海中总会第一个浮现这个改善。 场景二 “组长,这条产线我本来策划员工从手工作业更改成全自动产线,策划报告和整个方案全部理好了,但是物控却通知我明年这个产品就断点了,白白浪费了我大半个月的时间”,这是我任职IE组长之后,一名IE工程师对我说的话。 在我任职期间,面试了很多同行业或者是跨行业的IE人员,但是绝大部分人对于改善开展都缺乏逻辑性和系统性,下面我会对我理解的逻辑性和系统性进行讲解: 所谓逻辑性,最简单的一个问题就是:我为什么要对这条产线进行改善? 说到这里可能大家都会说,因为这条产线的需求量大、交货紧急,所以开展这条产线。那再问一个问题,是不是只有这条产线需求量大、交货紧急,其他产线都不存在这样的问题吗?可能问到这里一部分人就回答不上来了。 目前国内的制造型企业产品种类繁多,客户的需求也在不断的变化,可能这个月我们疲于交付的产品到下个月需求量就会骤降,那么我们要通过什么样的方式才能有逻辑、有目的的开展改善,把钢用在刀刃上那?我的建议是进行PQ(产品数量)分析。 我们拉取公司或者车间近一年来每种产品的月度客户需求量,作为我们的基础数据,通过累加的方式,得到每种产品的年度需求量,并进行从大到小排序,这样我们就可以得到一个关于产品数量的柏拉图,我们记录下占比前80%的产品,之后我们再通过物控部或市场部的产品预测需求,来对我们之前得到的前80%的产品进行纠正。纠正的目的在于明确我们前面得到的这些产品在后续的生产中销量依然可观。在这个过程当中,可能会有一些产线被筛选掉,但这不要紧,因为我们只要能够得到3-4条在去年的生产中销量很高,在后续的订单预测中也占较大比重的产线即可,而这3-4条产线,就是我们本月需要重点关注的产线。 当然,我们还可以对这3-4条产线进行进一步筛选,方法就是:针对每条产线,列出去年每个月份的产品需求量,对比今年的月份,横向、纵向对比一下,这样可以更好的指导我们改善的方向。 需要大家注意一点,那就是PQ分析出的产线只能说是比较有改善潜力的产线,不一定是后续量最大的产线,因为到底哪款产品会大卖,可能我们的客户也不确定。 说完了逻辑性,我们再来聊聊系统性; 所谓系统性,个人理解就是:我明确了要改善哪条产线,但是我不知道我所做的改善是不是很全面、很系统?是不是比我改善经验更足的人来做这条产线的改善,就会发现一些我发现不了的问题点? 对于IE工程师来说,改善经验至关重要的,它会在你进行产线改善时,更快的让你发现问题点。但是“IE七大手法”中的“防呆法”告诉我们,我们要让产线达到“员工不具备较高的技能也不会做错”的水平,那我们能否使用同样的方法来要求自己那? 对于我们公司来讲,绝大部分都是学校刚刚毕业的本科生,实战经验几乎为零。对于这类改善人员,如若没有系统的改善方式,他们的改善工作会非常难以开展,若全部由我一一指导,我也没有太多的精力,我的方法是运用“作业单元改善”工具: 该工具共包括现场布局分析,产线节拍图,程序分析等几部分组成,其中: 1、现场布局分析的内容包括:员工操作、搬运的移动距离(以mm为单位)、转身角度、动作等级等,这个表单的目的主要是为了让改善人员发现员工的搬运以及动作浪费; 2、产线节拍图可以帮助我们找出整条产线的瓶颈所在,明确改善方向。找出瓶颈工序后,我们就需要做下一步——程序分析; 3、程序分析是使用固定的表单格式记录下瓶颈工序在一个CT内的作业内容以及其对应的作业时间,并对每个细分的内容进行动作分类及增值判定,目的是找出制程浪费。只要我们的程序分析够详细,那么就不会错过任何一个浪费点和改善的可能。 通过“PQ分析”和“作业单元改善”这两种工具的运用,我们可以确保当前开展的产线就是我们最需要开展的产线,而且我们所开展的改善也能覆盖到绝大部分的问题点,只要这样我们才能说我们的改善开展是有逻辑性和系统性的。 场景三 “吴工,我们车间的产品种类属于多品种小批量,而且都是手工装配作业,公司领导今年给我定了人员节省10%的要求,能否帮我想想办法达到?” 对于手工装配类产线,最需要解决也最容易出成绩的就是“提升产线线平衡率”。但是很多人在做线平衡的时候,通常会去测产线的现状生产情况,并根据现状情况来制定改善方案,这种方法存在如下几个弊端: 1、现状人员作业技能参差不齐,导致按照当前的数据做了线平衡方案,但当员工技能提升后,又需要重新做线平衡方案; 2、老员工做相同工作量的作业时间会比新员工短,如果单纯从作业时间上来平衡,那么可能老员工已经承担了多于新员工工作量的内容,但是还要再继续分担工作任务,导致员工产生负面情绪; 3、每次测得的数据无法有效保存下来,导致有类似的新产品生产时无法提供数据支持。 我目前的做法是采用PTS(既定时间标准)来进行线平衡方案的排布(此种方法是在MOD法基础上衍变的更适用于我司的方法): 首先统计目前所有的手工装配类产品明细并明确所有产品的生产工序,再细分每一道工序所使用的物料明细,之后测定每一道工序使用该物料作业的最小颗粒度的时间,最后根据最小颗粒度数据进行线平衡方案的排布。 举个例子:假设我们要对一根线束进行缠胶带作业,而我们的胶带分为9mm、14mm、20mm宽等多种规格,那么员工在使用不同物料缠50mm长的线束时,时间肯定会不同。我们可以把50mm这个长度作为缠胶带的最小颗粒度,并让中等技能熟练的员工使用不同物料分别操作10次左右,取每种物料作业时间的平衡值作为该工序生产该物料的最小颗粒度时间。再把所有最小颗粒度时间统计完成后,建立产品最小颗粒度数据库。目的在于我们可以根据产品结构,找出生产该产品所对应的最小颗粒度数据,并进行累加算出该产品的预计生产周期。再根据物控部提供的客户需求,来计算所需线平衡排配人数。公式表示如下: 产品最小颗粒度累加时间/TT=线平衡排配人数; 接下来,我们再按照生产工艺流程及其对应的最小颗粒度时间进行工作量的时间累加,保证每名员工的理论CT不超过TT,排配出每名操作人员的工作内容。 此种方式有以下几点优势: 1、根据理论数据排布线平衡方案,可以保证线平衡率最高; 2、积累数据库信息,无论是长期未生产的产品还是与老产品类似的新产品都能起到数据支持(对于不在数据库中的产品工序或物料需进行持续更新); 3、对每个最小颗粒度时间进行再次优化提供数据支持。 接下来谈一下,如何使用“学习曲线”来解决新员工影响产线的理论生产周期。 “学习曲线”最早应用于美国的航空航天事业上,当时的美国人发现随着员工组装的飞机数量增多,每台飞机的组装时间伴随着一定的规律减少,当时他们便提出了“学习曲线”这一概念,并随之提出了相关的计算公式,以便通过数据来衡量员工的学习情况。 再了解这个方法之后,我结合本公司的实际情况,简化了计算方法,公式如下: Y = a * K n Y:第x个产品所需的工时; a:第1个产品所需的工时; K:该员工的学习率; x:2n,即n=log2x 首先,使用学习曲线的前提条件是,新员工或者新产线,因为只有“新”,才会有学习的存在,如果是明星产品和熟练员工,那么这个工具起到的意义不大; 其次,通过秒表测时法或者VTR分析法,测出员工做第1个产品所需的时间,也就是公式中的a; 然后再测量第2个、4个、8个产品生产所需的时间。之所以这样测量,是为了保证员工有充足的学习过程; 之后,将测得的4组数据,用后一个数与前一个数两两相比,得到学习率K,当然在计算时会出现几个数据不一致的情况,我们可以取平均值、最大值或最小值,这要根据每个公司的实际情况来定; 最后,我们得到了所需的数据,那么我们将数据套入公式进行描点、绘线,就得到了学习曲线,如图三所示: 
图3 得到学习曲线之后,我们再继续测定该员工生产第2n个产品时,是否按照曲线上的时间完成。如果完成时间在曲线之上,代表该员工没有按照既定的学习率去进步,那么车间需要与该员工谈话、沟通,告知其目前的状态,并了解没有达到的原因,对症下药、解决问题。如果该员工的时间在曲线下方,那么代表该员工超水平完成了工作,车间可以嘉奖该员工,并作为后续的班组长储备起来。 另外,有一点需要注意,员工的作业时间是不可能随着所做产品数量的增加,无限制的下降,那下降到哪一个基准为止哪? 这就要回到我们最初使用学习曲线的用途——排布产线线平衡方案; 在前面,我们已经得到了所生产产品的最小颗粒度时间,那么对于员工所做的工序,只需要从数据库中找到对应的工序,并累加时间就能得到该工序理论的生产周期,那么这个时间就是该员工要达到的目标,我们可以从表中了解到,该员工在正常状态下,需要多久能达到这个目标。 再补充一点,我们在测最小颗粒度的时候,采用的是中等熟练员工,而不是熟练员工。原因是培养熟练员工时间较长,对于大部分企业来讲,一线员工的流失率又无法控制,所以选择中等熟练员工的时间来排线平衡方案,会更容易出效果。当然对于员工忠诚度很高的企业就另当别论了。 关于学习曲线,还有很多可以分享的内容,比如员工操作的A工序还在学习过程中,被调去做不同于A工序类型的B工序,经过一段时间又回到A工序,那么该员工的学习曲线如何变化?或是在员工学习的过程中,影响到产线的线平衡方案,导致没有办法按照节拍交付,我们又该如何处理?等等问题,由于篇幅有限,就不一一介绍了,如果各位有兴趣的话,不妨自己实际操作一下。 对于绝大多数的制造型企业,大家都在“勒着腰带”生活,而企业的IE人员就需要持续改进、开源节流。只有不断的消除浪费、创造价值,企业才能有扎实的根基去创造更大的财富。 |